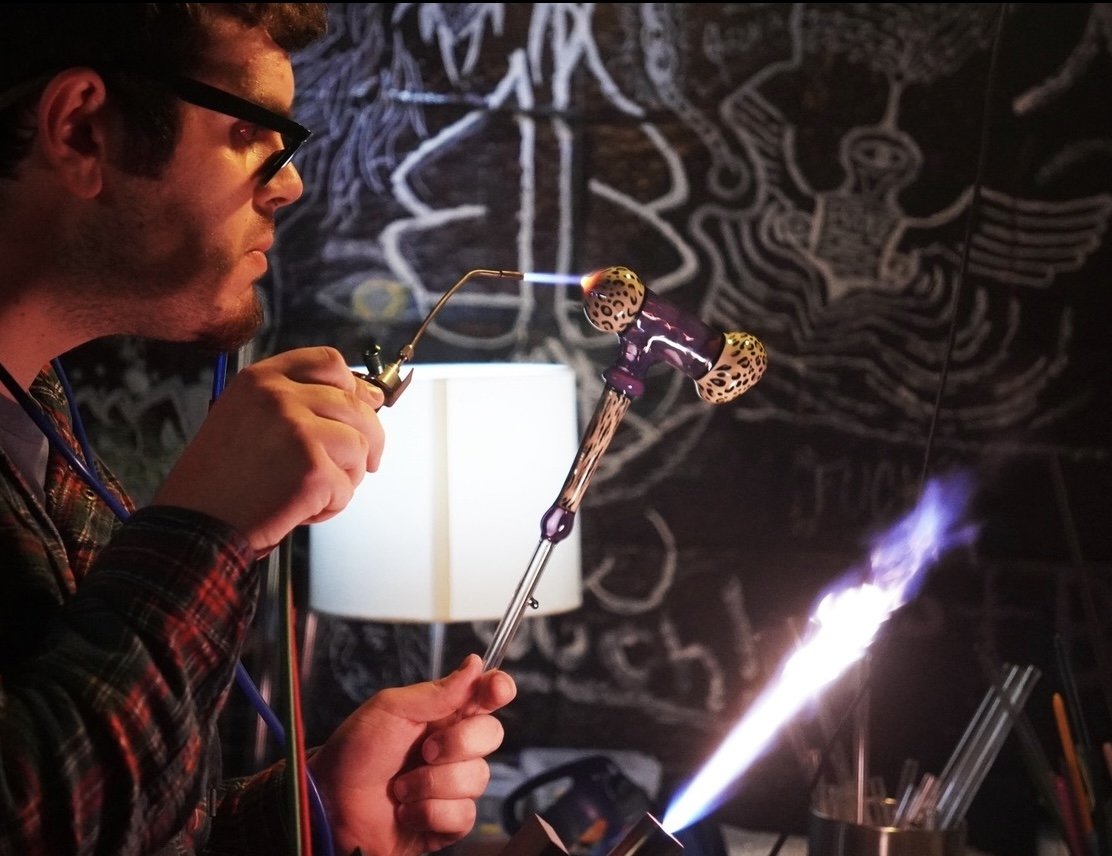
About Me:
Cameron Ure is a Scientific Glassblower currently based in Portland, Oregon. He began working with glass in Eugene, Oregon in 2019 while pursuing his undergraduate degree at the University of Oregon. After taking a marble-making class at the UO Craft Center, Cameron quickly sought out further instruction from a local glass artist in order to pursue the medium and begin his career path working with borosilicate glass. This ignited the glass journey that led to the three S’s: Salem, Switzerland, and Simone.
After graduating from the University of Oregon in 2020, Cameron left Eugene and moved to Southern New Jersey, where he began the Scientific Glass and Technology program at Salem Community College, the only university with such a program. There he was introduced to scientific glass, and all of the various techniques and methodologies used in the fabrication process. Seeing where these skills and techniques could take the glass, Cameron decided to dedicate his time and energy towards scientific glass, working in the school’s studio most days from open until close.
This dedication quickly yielded results, not only in his abilities with the craft, but also with other learning/career opportunities. After the first two semesters, Cameron had earned a position as the Flameworking Intern at the Corning Museum of Glass, where he provided flameworking demonstrations to guests of the museum, and also received training under master goblet maker, Eric Goldschmidt.
During his final semester at SCC, Cameron received a job offer from Büchi AG, a scientific glass company operating out of Switzerland. Upon completion of the degree, Cameron moved from Southern New Jersey to Zürich, Switzerland, where he began working full-time as a scientific glassblower.
In this position, he was introduced to a new level of flameworking, commonly working with tubes ranging from 150mm to 465mm in diameter to make customized apparatus used in the pharmaceutical industry. The larger scale of work; however, did not minimize the importance of dimensions. Working in the scientific industry further stressed the importance of precision, as extremely tight tolerances of measurement had to be navigated. This experience allowed Cameron to gain a better understanding of working with borosilicate glass on a much larger scale, while he also continued to practice and experiment with glass in his free time at a local studio in Zürich.
After a little over a year of working in Switzerland, Cameron decided to move back to the United States, setting up in a shop in Portland, Oregon, where he continued exploring his goals and interests with borosilicate glass.
Shortly thereafter, master glassblower Simone Crestani asked Cameron to work for him in Italy on a short-term contract. There, he learned the skills to adapt to the pace of production work, making thousands of components for borosilicate glass chandeliers and lighting installations, in addition to other varying projects employing a Venetian style of flameworking.
Cameron now lives in Boston, MA, where he is actively pursuing his own goals and interests with glass. His work focuses on creating unique and high quality glass objets that both serve a purpose and provide an engaging narrative.
Collaboration with Carl Natalino (@babygorillaglass)
About the Process and Material:
The process of flameworking, or lampworking, utilizes a mounted burner that combines gas (most commonly propane or natural gas) and oxygen to actively shape rods and tubes within a flame. It is a process unlike soft glass furnace work, where molten glass is gathered from a hot furnace and shaped outside of the heat source. This is the most commonly known method of glassblowing, and while there are many similar working characteristics, this process requires an entirely different set of skills and abilities.
Flameworking can be done with a number of different glasses (there are over 10,000 types of glass); however, I work with borosilicate glass almost exclusively. Borosilicate glass is a combination of silica, boron, sodium, and aluminum. Different metals can also be added to the glass as colorant, such as silver. This type of glass is most commonly used to produce lab apparatus for scientific purposes, though it is also commonly used in lighting fixtures, cookware, and functional art.
Working with glass is a very labor intensive process, that requires a lot of patience. The heat required to manipulate the glass is intense, and can be extreme as the size of a piece may increase. The glass, particularly when cut, can be very sharp and cause serious cuts easily. It is extremely important to observe proper safety precautions at all times when working with glass and the required equipment.
Glass is unlike any other material and requires many hours of practice just to move beyond the beginner level. The fragility of glass and temperamental working characteristics will teach its user humility, particularly in the beginning as the hard lessons are frequently learned through failure. A piece can be lost at any point in the process, even once its finished. Glass teaches the maker and beholder to respect the material, and cherish the outcome.
Some of the most common tools for a glassblower are steel tweezers, graphite rods and paddles, blowhoses to attach to glass tubes, and of course protective eyewear. Didymium glasses are probably the most important tool for both safety, and to be able to actually see the glass. The didymium filter on the glass lens filters out sodium flare, which is a bright orange glow emitted by the sodium being burnt out of the glass when in the flame. There are a variety of other tools to be used, most commonly made from steel and/or graphite, which hold up against the heat of molten glass relatively well. One other important tool, most commonly used in the scientific glass industry is a glass lathe, which will turn the glass, allowing for more heat and tooling application by the maker.
One of the greatest challenges of working with glass is dealing with stress. I don’t just mean the feeling of stress as you reach the finish line of a piece you’ve put 20 hours of work into and could still crack and be ruined. In fact, I don’t really mean that at all. Glass will crack at its weakest point, or where the most stress is contained. Stress can occur from a number of things, both in the fabrication process, as well as after it has been made. These causes may include some sort of pressure or impact, a drastic and sudden change in temperature, an improper connection, or some sort of flaw within the raw material. The most common cause of cracking during the fabrication process is improper heat. A little bit of heat causes the glass to expand, and a lot of heat causes the glass to contract. So, if the glass is not evenly heated, then some areas want to expand or contract, while other areas are stagnant. This uneven expanding and contracting causes a pulling tension within the glass molecules that may lead to a crack.
One of the primary methods to remove stress from glass is through annealing. Annealing is the process of slowly cooling the glass in a controlled environment in order to remove stress within the glass. Annealing is most commonly done with the use of a kiln. By using a kiln, the glass can all be heated to the same temperature which cause the molecules within the glass to stabilize and relax. Annealing can also be done using a gas-heavy flame to gently heat the glass to all the same temperature, then placed in an insulated environment, such as a container full of vermiculite. However, a kiln is always going to be a more secure method of annealing, as long as it is used correctly.
Artist Statement:
I always think it’s about the end product when making a piece of glass, but it’s not. In fact, it almost never is. I’m usually disappointed when I finally finish a piece. Not because of the outcome, but because it’s over. I guess the cool thing about that is that I get to start over again and again and again. I’m not excited to open the kiln the next morning, I’m excited to turn it on again.
It’s hard to summarize your work with a statement, especially when you want your work to encapsulate so many different techniques and concepts. But if I had to, I would say it’s about creating unique glass objects with a purpose and a story, and that were crafted to be cherished. I hope every design works well, and is treasured in the eyes of the beholder, but really I was just having a kick-ass time making it.